Parker Hannifin Purpose in Action Project
An exposé on the groundbreaking work WCHS ag students and disability advocates have been doing.
Over the past seven months, WCHS students involved with Mr. Richardson’s agriculture classes have teamed up with disability advocates in the school, trying to create a universal work cell for a factory in Lexington called Parker Hannifin. Parker is a global manufacturer of o-rings, which helps seal air inside of everyday things like cans, to things as specialized as scuba gear, jets, rockets, and more.
Parker is looking to make their facilities more accessible for all so that people from all walks of life will be able to have the same opportunities. We were just one of sixteen groups contacted about this opportunity to make the workplace an equal setting. One of the others is Berea Makerspace, a staple for the creative minds in Berea. They were the only other ones who accepted the challenge. Both groups presented our final designs for the project on April 26th at EKU.
Below is a gallery that details the process of the project, what it will do, and the outcome.
To conclude, this experience has been very rewarding and eye-opening for me. I’m stoked to see what the future holds for universal designing, and in that same vein, what the future holds for people with disabilities in the workplace. Thanks for reading.
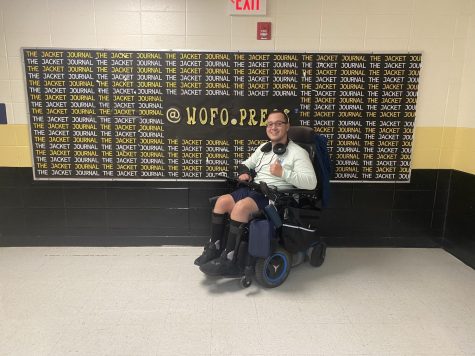
Gavin is a senior at Woodford County High School. He is in his second and final year as a Jacket Journal writer and in his first year of Channel 4 contribution....